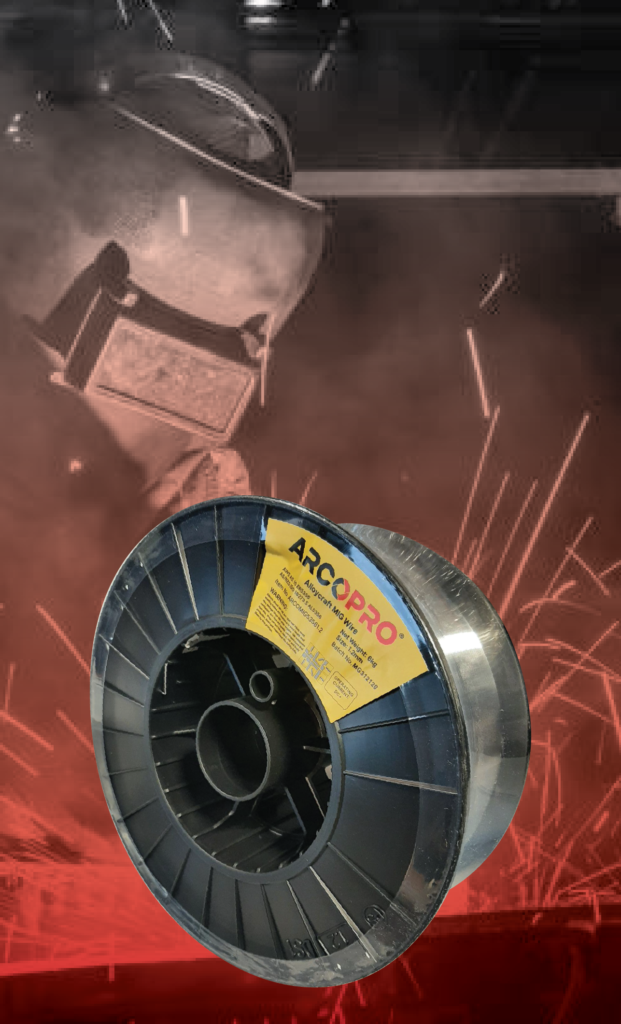
ArcoPro Aluminium MIG Wire 5356 is a premium welding wire engineered to meet the rigorous demands of various industries. Renowned for its exceptional quality, versatility, and compliance with international standards, it has become a trusted choice for professionals in sectors such as truck and tank storage, marine manufacturing, agricultural fabrication, automotive production, and beyond. Extensively tested within New Zealand’s industrial landscape, this high-performance MIG wire consistently delivers reliable results. Below, we delve into its applications across these industries and outline the specifications that ensure its superior performance.
APPLICATION ACROSS KEY INDUSTRIES:
Truck and Tank Storage Panels
The truck and tank storage industry requires durable and corrosion-resistant materials to ensure the longevity and safety of storage systems. ArcoPro Aluminium MIG Wire 5356 is ideal for welding aluminium panels and tanks due to its excellent corrosion resistance, particularly in harsh environments where exposure to moisture or chemicals is common. Its compatibility with 100% Argon or Argon/Helium shielding gas ensures clean, high-quality welds with minimal spatter, making it suitable for welding in all positions (except vertical-down).
Marine Boat and Ship Manufacturing
Marine environments demand materials that can withstand saltwater corrosion and extreme conditions. ArcoPro MIG Wire 5356, with its classification under ABS, LR, and RINA registers, meets the rigorous standards required for shipbuilding and boat manufacturing. The wire’s ability to weld aluminium alloys such as AL5456 ensures strong and reliable joints in hulls, decks, and structural components. Its 1.2mm diameter and compatibility with DC welding current provide precision and efficiency, making it a go-to solution for marine applications.
Agricultural Fabrication
In agricultural fabrication, equipment and structures must endure heavy use and exposure to the elements. ArcoPro Aluminium MIG Wire 5356 offers excellent strength and durability, making it perfect for welding aluminium components in machinery, storage bins, and irrigation systems. Its 6kg spool size (D270) ensures extended welding sessions with fewer interruptions, increasing productivity in large-scale fabrication projects.
Automotive Industry
The automotive sector relies on lightweight yet strong materials to improve vehicle performance and fuel efficiency. ArcoPro MIG Wire 5356 is widely used in welding aluminium parts such as frames, panels, and structural components. Its conformance to AWS A5.10 ER5356 and AS/NZS ISO 18273 AL5456 standards guarantees high-quality welds that meet industry requirements. The wire’s versatility in all welding positions (except vertical-down) ensures adaptability to various automotive manufacturing processes.
Walkways and Grating Applications
Walkways and grating systems require durable, lightweight, and corrosion-resistant materials. ArcoPro Aluminium MIG Wire 5356 is ideal for welding aluminium grating and walkway components, providing strong, clean welds that enhance structural integrity. Its compatibility with Argon or Argon/Helium shielding gases ensures smooth welds with minimal porosity, making it a reliable choice for fabricators in this sector.
General Fabrication and Repair
For general fabrication and repair work, versatility is key. ArcoPro MIG Wire 5356’s ability to weld in multiple positions and its compatibility with standard shielding gases make it suitable for a wide range of applications. Whether repairing aluminium structures or fabricating new components, this MIG wire delivers consistent, high-quality results.
Welding Aluminium Alloys
ArcoPro Aluminium MIG Wire 5356 is specifically designed for welding aluminium alloys such as AL5456, which are commonly used in industries requiring high strength and corrosion resistance. Its classification under ABS, LR, and RINA registers ensures compliance with international standards, making it a trusted choice for critical applications.
Specifications of ArcoPro Aluminium MIG Wire 5356
- Wire Diameter: 1.2mm
- Spool Size: D270 (6kg capacity)
- Welding Current: DC
- Shielding Gas: 100% Argon or Argon/Helium mix
- Standards: AWS A5.10 ER5356, AS/NZS ISO 18273 AL5456
- Classification Registers: ABS, LR, RINA
- Welding Positions: All positions except vertical-down
Why Choose ArcoPro Aluminium MIG Wire 5356?
ArcoPro Aluminium MIG Wire 5356 stands out for its exceptional performance, reliability, and adherence to international standards. Its ability to deliver strong, corrosion-resistant welds across multiple industries makes it a versatile and cost-effective solution for professionals. Whether you’re fabricating lightweight automotive components or constructing durable marine vessels, ArcoPro MIG Wire ensures precision and quality in every weld.
Choose ArcoPro Aluminium MIG Wire 5356 for your next welding project and experience the difference in performance and durability.